WIRE ROPE INSPECTION AND REMOVAL CRITERIA
Any wire rope in use should be inspected on a regular basis. You have too much at stake in lives and equipment to ignore thorough examination of the rope at prescribed intervals.
The purpose of inspection is to accurately estimate the service life and strength remaining in a rope so that maximum service can be had within the limits of safety. Results of the inspection should be recorded to provide a history of rope performance on a particular job.
On most jobs wire rope must be replaced before there is any risk of failure. A rope broken in service can destroy machinery and curtail production. It can also kill.
Because of the great responsibility involved in ensuring safe rigging on equipment, the person assigned to inspect should know wire rope and its operation thoroughly. Inspections should be made periodically and before each use, and the results recorded.
When inspecting the rope, the condition of the drum, sheaves, guards, cable clamps and other end fittings should be noted. The condition of these parts affects rope wear: any defects detected should be repaired.
To ensure rope soundness between inspections, all workers should participate. The operator can be most helpful by watching the ropes under his control. If any accident involving the ropes occurs, the operator should immediately shut down his equipment and report the accident to his supervisor. The equipment should be inspected before resuming operation.
The Occupational Safety and Health Act has made periodic inspection mandatory for most wire rope applications. If you need help locating the regulations that apply to your application, please give our rigging experts a call.
Frequent Inspection
All running ropes and slings in service should be visually inspected once each working day. A visual inspection consists of observation of all rope and end connections which can reasonably be expected to be in use during daily operations. These visual observations should be concerned with discovering damage such as listed below, which may be an immediate hazard:
- Distortion of the rope such as kinking, crushing, unstranding, birdcaging, main strand displacement or core protrusion.
- General corrosion.
- Number, distribution, and type of visible broken wires.
- Lack of lubrication
Special care should be taken when inspecting portions subjected to rapid deterioration such as flange points, crossover points and repetitive pickup points on drums.
Special care should also be taken when inspecting certain ropes such as:
- Rotation resistant ropes such as 19x7 and 8x19, because of their higher susceptibility to damage and increased deterioration when working on equipment with limited design parameters.
- Boom Hoist Ropes because of the difficulties of inspection and important nature of these ropes.
When damage is discovered, the rope should either be removed from service or given an inspection as detailed in the section below.
Periodic Inspection
The inspection frequency should be determined by a qualified person and should be based on such factors as: expected rope life as determined by experience on the particular installation or similar installations, severity of environment, percentage of capacity lifts, frequency rates of operation, and exposure to shock loads.
Periodic inspections with a signed report should be performed by an appointed or authorized person. This inspection should cover the entire length of rope. The individual wires in the strands of the rope should be visible to this person during the inspection. Any deterioration resulting in appreciable loss of original strength, such as described below, should be noted and a determination made as to whether further use of the rope would constitute a hazard:
- Distortion of the rope such as kinking, birdcaging, crushing, unstranding, main strand displacement, or core protrusion.
- Reduction of rope diameter below normal diameter due to loss of core support, internal or external corrosion, or wear of outside wires.
- Severely corroded, cracked, bent, worn, or improperly applied end connections.
Special care should be taken when inspecting portions subjected to rapid deterioration such as the following:
- Portions in contact with saddles, equalizer sheaves, or other sheaves where rope travel is limited.
- Portions of the rope at or near terminal ends where corroded or broken wires may protrude.
O.S.H.A. (A.N.S.I.) Removal Criteria 5. A.N.S.I. Safety Codes, Standards and Requirements
Rope MUST be removed from service when diameter loss or wire breakage occurs as follows:
A.N.S.I. Number |
Equipment |
Number of Broken Wires in Running Ropes |
Number of Broken Wires in Standing Ropes | ||
---|---|---|---|---|---|
In One Rope Lay |
In One Strand |
In One Rope Lay |
At End Connection | ||
B30.2 |
Overhead and Gantry Cranes |
12 |
4 |
Not Specified |
Not Specified |
B30.4 |
Portal, Tower and Pillar Cranes |
6 |
3 |
3 |
2 |
B30.5 |
Crawler, Locomotive, and Truck Cranes |
6 |
3 |
3 |
2 |
B30.6 |
Derricks |
6 |
3 |
3 |
2 |
B30.7 |
Base Mounted Drum Hoists |
6 |
3 |
3 |
2 |
B30.8 |
Floating Cranes and Derricks |
6 |
3 |
3 |
2 |
A10.4 |
Personnel Hoists |
6* |
3 |
2* |
2 |
A10.5 |
Material Hoists |
6* |
Not Specified |
Not Specified |
*Also remove for 1 valley break. OSHA requires monthly record keeping of wire rope condition.
Service life of wire rope is dependent on several factors, including environmental conditions, frequency of operation, and weight of lifts.
In this respect, continued use depends largely upon good judgment by an appointed or authorized person in evaluating remaining strength in a used rope, after allowance for deterioration disclosed by inspection. Continued rope operation depends upon this remaining strength.
Conditions such as the following should be sufficient reason for questioning continued use of the rope or increasing the frequency of inspection:
- In running ropes, six randomly distributed broken wires in one lay, or three broken wires in one strand in one lay. (The number of wire breaks beyond which concern should be shown varies with rope usage and construction. For general application 6 and 3 are satisfactory. Ropes used on overhead and gantry cranes (as defined in ASME B-30, 2-1983)can be inspected to 12 and 4. Rotation resistant ropes should be inspected to 4 and 2.)
- One outer wire broken at the contact point with the core of the rope which has worked its way out of the rope structure and protrudes or loops out from the rope structure.
- Wear of one-third the original diameter of outside individual wires.
- Kinking, crushing, birdcaging, or any other damage resulting in distortion of the rope structure.
- Evidence of any heat damage from any cause.
- Valley breaks.
- In standing ropes, more than two broken wires in one lay in section beyond end connections or more than one broken wire at an end connection.
- Reductions from nominal rope diameter of more than:
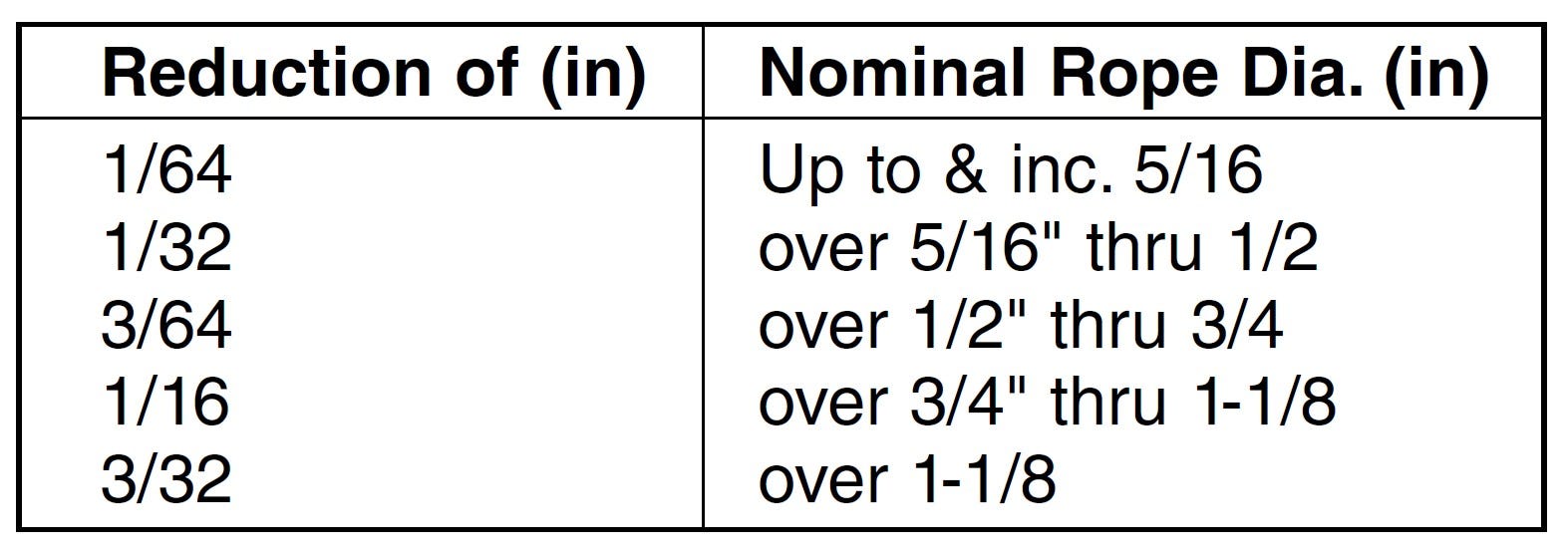
Replacement rope shall have a strength rating at least as great as the original rope furnished by the equipment manufacturer or as originally specified. Any deviation from the original size, grade, or construction shall be specified by the equipment manufacturer, original design engineer, or a qualified person.
Ropes Not In Regular Use
All rope which has been idle for a period of a month or more due to shutdown or storage of equipment on which it is installed should be given inspections as previously described before being placed in service. This inspection should be for all types of deterioration and should be performed by an appointed or authorized person.
Inspection Records
Frequent Inspection: No records required.
Periodic Inspection: In order to establish data as a basis for judging the proper time for replacement a signed report of rope condition at each periodic inspection should be kept on file. This report should include points of deterioration previously described.
A long range inspection program should be established and include records of examination of ropes removed from service so a relationship can be established between visual observation and actual condition of the internal structure.
How to Measure Wire Rope Diameter
Ropes and sheave grooves must be precisely fitted to each other to get the most service out of your wire rope dollar. Make measurement of rope diameter a normal part of your inspection program.
There's only one right way to measure rope diameter: use machinist's calipers and be sure to measure the widest diameter. These drawings compare the right way with the wrong way.
This method is not only useful for measuring the diameter of a new rope, but also for determining the amount of wear and compression that has occurred while the rope has been in use. Accurate recording of this information is essential in helping to decide when to replace wire rope.
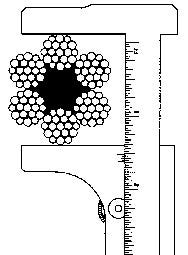
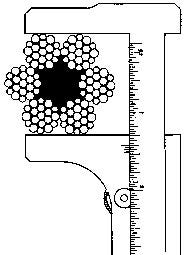
Right Way. Set the machinist's caliper to read the widest diameter. Vernier scale reads to 1/128th of an inch.
Wrong Way. This is the wrong way to measure wire rope diameter. Widest diameter is not being used.
Sheave Inspection
Inspection of sheaves is a relatively simple, yet very vital task. A sheave groove gauge, usually obtainable from a wire rope manufacturer, is used to check the grooves in a sheave. Hold the gauge perpendicular to the surface of the groove to observe properly the groove size and contour, as in this illustration.
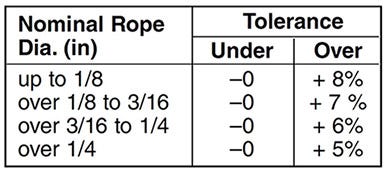
Photo shows new gauge and worn sheave. This new gauge is designed with one-half the allowable oversize (see table).
Using the new gauge, when you do not see light, the sheave is OK. When you do see light under the new gauge, the sheave should be replaced.
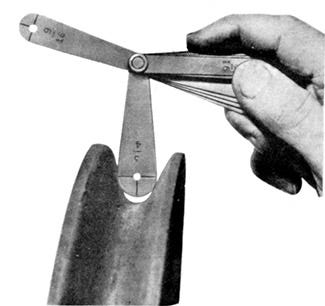
Sheaves should be checked for:
- Correct groove diameter
- Roundness or contour to give proper support to the rope
- Small holes, cracks, uneven surfaces, or other defects that might be detrimental to the rope
- Extreme deep wear
A sheave should also be checked to make sure it turns freely, is properly aligned, has no broken or cracked flanges, and has bearings that work properly.
Drum Inspection
Drums should also be inspected for signs of wear that could damage rope.
Plain-faced or smooth drums can develop grooves or impressions that prevent rope from winding properly. Repair by resurfacing the face or replacing the lagging.
Scrubbing will occur if the rope tends to close wind. If the tendency is to open winding, the rope will encounter abnormal abuse as the second layer forces itself down between the open wraps of the first layer on the drum.
Operating with a smooth drum calls for special care. Be sure the rope is always tightly wound and thread laid on the first layer. Any loosening of the line is easily observed as the winding will be bad and the rope will be coming off with a series of “bad spots.”
Grooved drums should be examined for tight or corrugated grooves and for differences in depth or pitch that could damage the second and subsequent layers. Worn grooves can develop extremely sharp edges that shave away small particles of steel from the rope. Correct this condition by grinding or filing a radius to replace the sharp edge.
Drum flanges, as well as the starter, filler and riser strips, should be checked. Excessive wear here often causes unnecessary rope abuse at the change of layers and cross-over points.
Other places of contact such as rollers, scrub boards, guides and end attachments should also be inspected.