WIRE ROPE STRENGTH DESIGN FACTORS AND PHYSICAL PROPERTIES
The rope strength design factor is the ratio of the rated strength of the rope to its operating stress. If a particular rope has a rated strength of 100,000 lbs. and is working under an operating stress of 20,000 lbs., it has a rope strength design factor of 5. It is operating at one fifth or 20% of its rated strength.
Many codes refer to this factor as the "Safety Factor" which is a misleading term, since this ratio obviously does not include the many facets of an operation which must be considered in determining safety. Wire rope is an expendable item - a replacement part of a machine or installation. For economic and other reasons, some installations require rope to operate at high stress (low rope strength design factors). On some installations where high risk is involved, high rope strength design factors must be maintained.
However, operating and safety codes exist for most applications and these codes give specific factors for usage. When a machine is working and large dynamic loadings (shock loadings) are imparted to the rope, the rope strength design factor will be reduced which could result in overstressing of the rope. Reduced rope strength design factors frequently result in reduced service life of wire rope.
Wire Rope Strength Design Factor
Wire rope must have the strength required to handle the maximum load plus a design factor. The design factor is the ratio of the breaking strength of the rope to the maximum working load. To establish the proper design factor, several operating characteristics should be considered:
- Speed of operation
- Acceleration and deceleration
- Length of rope
- Number, size and location of sheaves and drums
- Rope attachments
- Conditions causing corrosion and abrasion
- Danger to human life and property.
Fatigue Resistance
Smaller wires are the key to bending performance when wire ropes are subjected to repeated bending over sheaves or drums. The more outer wires for a given size wire rope, the better the resistance to bending fatigue. The relative bending life factors of typical wire rope constructions are indicated in the table below.
Ropes having a large number of small wires, however, should not be used where overwrapping on a drum takes place because they do not provide sufficient crush resistance.
Abrasion Resistance
Lang lay and large outer wires provide resistance to abrasion. The relationship between abrasion resistance and fatigue resistance is illustrated.
Crush Resistance
An IWRC (Independent Wire Rope Core) and large outer wires will provide best crush resistance. Constructex rope provides the best crush resistance of any wire rope.
Flexibility
Fiber core, lang lay and smaller wires provide a more flexible wire rope.
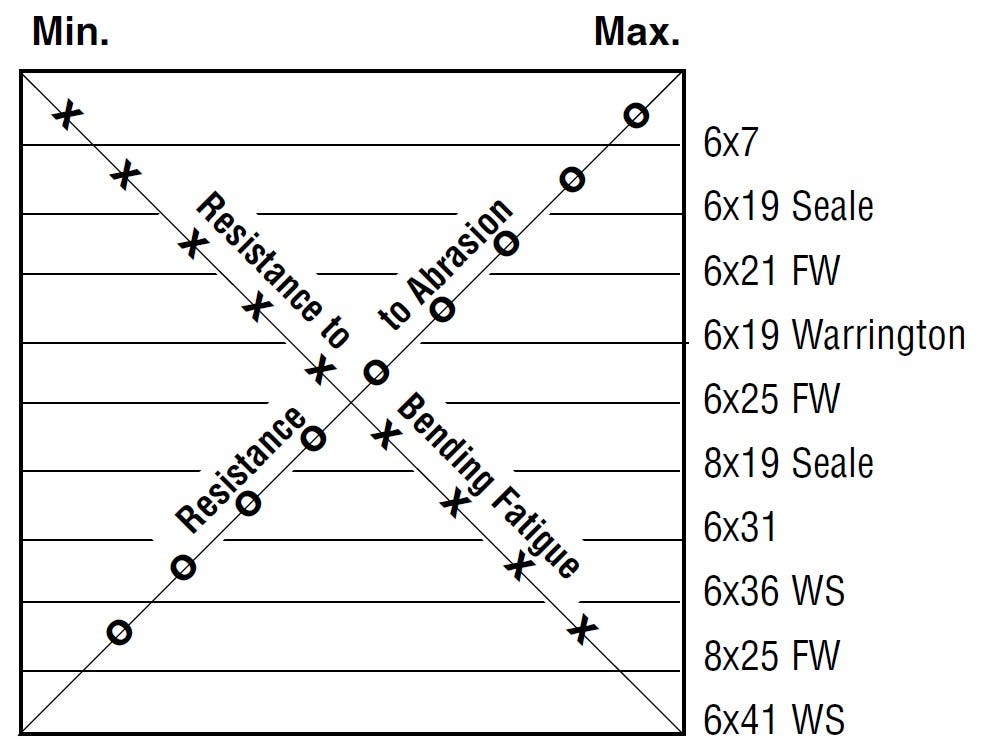
Constructional Stretch
When a load is applied to wire rope, the helically-laid wires and strands act in a constricting manner thereby compressing the core and bringing all the rope elements into closer contact. The result is a slight reduction in diameter and an accompanying lengthening of the rope.
Constructional stretch is influenced by the following factors:
- Type of core (fiber or steel)
- Rope construction (6x7, 6x25 FW, 6x41 WS, 8x19 S, etc.)
- Length of lay
- Material
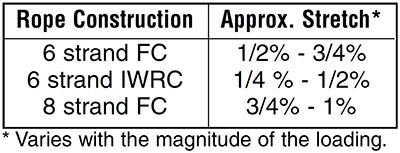
Ropes with wire strand core (WSC) or independent wire rope core (IWRC) have less constructional stretch than those with fiber core (FC). The reason for this is the fact that the steel cannot compress as much as the fiber core.
Usually, constructional stretch will cease at an early stage in the rope's life. However, some fiber core ropes, if lightly loaded (as in the case of elevator ropes), may display a degree of constructional stretch over a considerable portion of their life.
A definite value for determining constructional stretch cannot be assigned since it is influenced by several factors. The following table gives some idea of the approximate stretch as a percentage of rope under load.