Wire Rope 101
Wire rope is a machine consisting of wires laid around a central core. This high strength, flexible piece of equipment is ideal for heavy lifting and positioning. With resistance to damage from heat, sunlight, chemicals, and water, wire rope is relied on for lifting applications around the world by the construction, industrial, mining, wind, military, and marine industries.
Our wire rope information guide, "Wire Rope 101," is a starting point for anyone wanting to learn the wire rope basics. It includes information about types of wire rope and their physical properties; wire rope lays and constructions; guidelines for inspection; common wire rope abuses and recommendations for use; wire rope cross sections; and a glossary of terms.
Hanes Supply has been splicing wire rope since 1930, and is a leading expert in the industry. For more information about selecting the right wire rope for your application, or how to most effectively and safely use your wire rope, please contact us at 1-888-426-3755.
What Is Wire Rope?
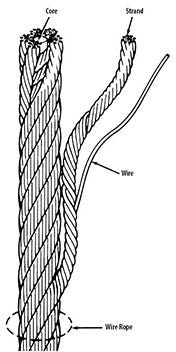
A wire rope is a piece of flexible, multi-wired, stranded machinery made of many precision parts. Usually a wire rope consists of a core member, around which a number of multi-wired strands are “laid” or helically bent.
There are two general types of cores for wire rope - fiber cores and wire cores. The fiber core may be made from natural or synthetic fibers. The wire core can be an Independent Wire Rope Core (IWRC), or a Strand Core (SC).
The purpose of the core is to provide support and maintain the position of the outer strands during operation. Any number of multi-wired strands may be laid around the core. The most popular arrangement is six strands around the core, as this combination gives the best balance.
The number of wires per strand may vary from 3 to 91, with the majority of wire ropes failing into the 7-wire, 19-wire, or 37- wire strand categories.
Lays of Wire Rope
“Lay” of a wire rope is simply a description of the way wires and strands are placed during construction. Right lay and left lay refer to the direction of strands.
Right lay means that the strands pass from left to right across the rope. Left lay means just the opposite: strands pass from right to left.
Regular lay and lang lay describe the way wires are placed within each strand. Regular lay means that wires in the strands are laid opposite in direction to the lay of the strands. Lang lay means that wires are laid in the same direction as the lay of the strands.
Most of the wire rope used is right lay, regular lay. This specification has the widest range of applications and meets the requirements of most equipment. In fact, other lay specifications are considered exceptions and must be requested when ordering.
Exceptions to the Rules
Lang lay is recommended for many excavating, construction, and mining applications, including draglines, hoist lines, dredgelines and other similar lines.
Here's why: Lang lay ropes are more flexible than regular lay ropes. They also have greater wearing surface per wire than regular lay ropes.
Where properly recommended, installed and used, lang lay ropes can be used to greater advantage than regular lay ropes. However, lang lay ropes are more susceptible to the abuses of bending over small diameter sheaves, pinching in undersize sheave grooves, crushing when winding on drums, and failing due to excessive rotation.
Left lay rope has greatest usage in oil fields on rod and tubing lines, blast hole rigs, and spudders where rotation of right lay rope would loosen couplings. The rotation of a left lay rope tightens a standard coupling.
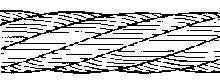
Left Lay - REGULAR LAY
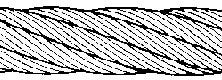
Right Lay - LANG LAY
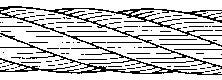
Right Lay - REGULAR LAY
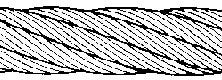
LEFT LAY - LANG LAY
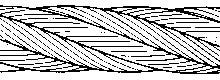
ALTERNATE RIGHT LAY
Wire Rope Strand Constructions
Wire ropes are composed of independent parts -- wires, strands and cores -- that continuously interact with each other during service.
Wire rope engineers design those parts in differing steel grades, finishes and a variety of constructions to attain the best balance of strength, abrasion resistance, crush resistance, bending fatigue resistance and corrosion resistance for each application.
To select the best wire rope for each application, one must know the required performance characteristics for the job and enough about wire rope design to select the optimum combination of wire rope properties.
Strands are designed with various combinations of wires and wire sizes to produce the desired resistance to fatigue and abrasion. Generally, a small number of large wires will be more abrasion resistant and less fatigue resistant than a large number of small wires.
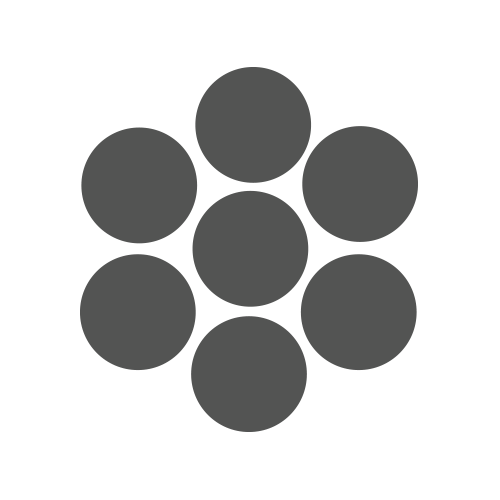
Single Size
The basic strand construction has wires of the same size wound around a center.
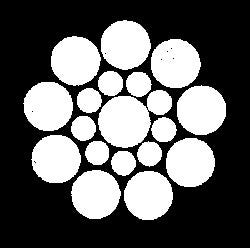
Seale
Large outer wires with the same number of smaller inner wires around a core wire. Provides excellent abrasion resistance but less fatigue resistance.
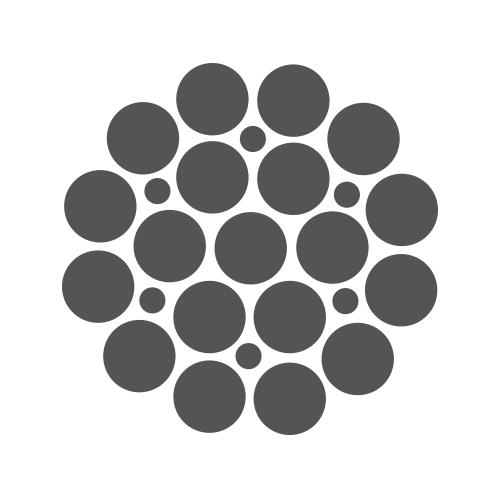
Filler Wire
Small wires fill spaces between large wires to produce crush resistance and a good balance of strength, flexibility and resistance to abrasion.
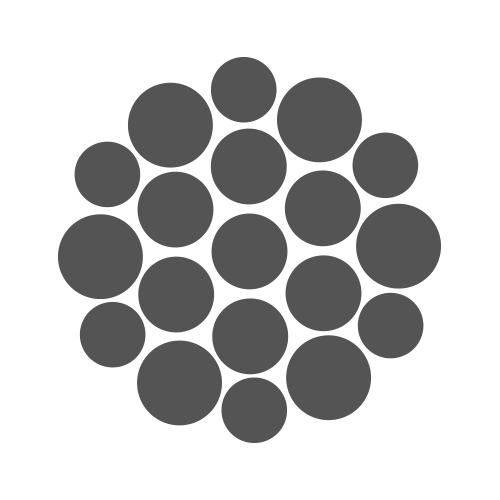
Warrington
Outer layer of alternately large and small wires provides good flexibility and strength but low abrasion and crush resistance.
Many commonly used wire ropes use combinations of these basic constructions. These strand designs can also be covered with one or more layers of uniform-sized wires to create a multiple operation rope.
Strand constructions affect the physical properties of wire rope, including strength, fatigue resistance, and abrasion resistance.
Some common combinations of these basic strand constructions include:
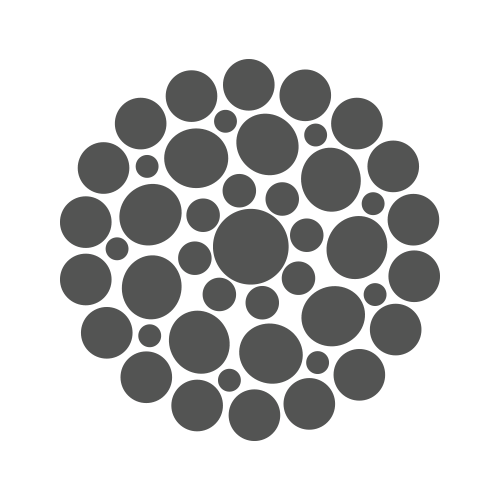
Seale Filler Wire
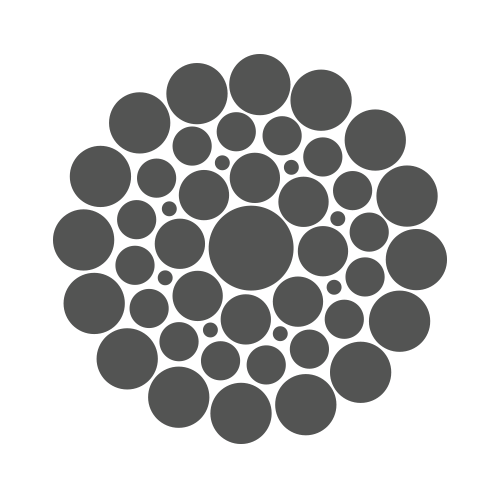
Filler Wire Seale
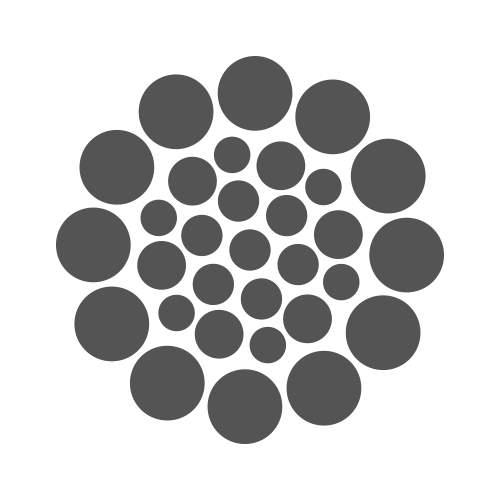
Warrington Seale
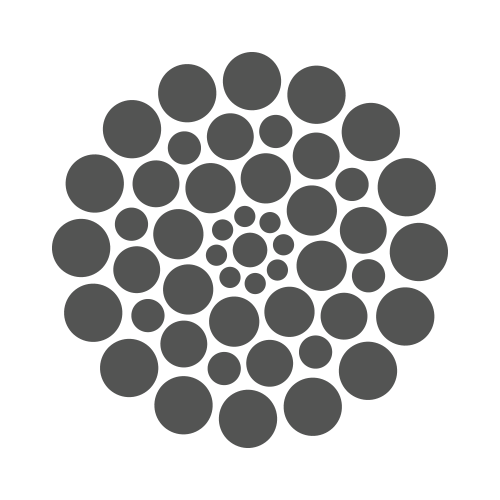
Seale Warrington Seale
Wire Rope Grades and Finishes
Bright finish is suitable for most applications. Galvanized finish is available for corrosive environments. Plastic jacketing is also available on some constructions.
The most common steel wire grades are: IPS (Improved Plow Steel), EIP (Extra Improved Plow Steel) and EEIP (Extra Extra Improved Plow Steel). Stainless Steels and other special grades are provided for special applications.
Most wire ropes are made with round wires. Both triangular and shaped wires are also used for special constructions. Generally, the higher the strength of the wire, the lower its ductility will be.